Dye printing is an important production process in textile industry. The traditional method of dye-sublimation involves a transfer paper, but in recent years systems have been developed that allow you to print directly onto fabric without using a transfer medium. This is known as direct disperse printing. This method has some advantages over the traditional one, but it also has its own set of issues that you need to be aware of.
A dye is an organic chemical compound that gives color to a fiber or textile. There are three different types of dyes: disperse, vat, and reactive. Disperse dyes are the most commonly used for printing on polyester fabrics, but there are other options as well. If you are looking for high-quality prints that look beautiful and offer exceptional wash fastness, then direct disperse printing is the way to go.
However, if you’re printing on cotton, it is not recommended to use this method. Cotton has a higher abrasion resistance than polyester, and it’s much easier to tear than other textiles. Disperse dyes don’t adhere very well to cotton, so they tend to rub off easily when you wash them. It’s best to choose a different dyeing process for cotton, such as a vat or disperse/reactive combination, if you want to print on it.
Direct disperse printing can be done on polyester and other synthetic fabric fibers, such as nylon. This printing process is more expensive than the traditional dye-sublimation method, but it offers the benefit of being able to print on both sides of the fabric. It’s ideal for a variety of uses, including home décor and soft signage. However, it is not suitable for apparel applications because the color-to-washfastness results aren’t bulletproof. It’s best to use other printing methods, such as pigment printing, if you want to print on clothing.
To make the inks for this method, you’ll need disperse dyes and polyethylene terephthalate (PET) film. You’ll also need a thickener to help the inks spread out evenly on the fabric. Natural gums, starch ethers, and modified locust bean gums are all good choices. Generally, the thickeners should have a high solid content and be suitable for steaming and thermofixation.
The inks are printed on the polyester fabric and PET film with an Epson R330 inkjet printer. The monochrome block patterns and 353 mm-wide straight lines were printed on the polyester fabric. The fabric and film were then steamed at 128oC (30 psi pressure) for 30 minutes, dried at 90oC for 1 minute, and thermofixed at 190oC for 10 seconds. The printed fabric was tested for color strength, rubbing fastness, and washing fastness.
The printed samples had a color strength of K/S 2.1 and a rubbing fastness grade of 3-4. The washing fastness of the polyester fabric reached grade 4-5. The new process reduced the washing and drying times by half compared to the conventional printing method and allowed for shorter production times. It also reduces the negative environmental impact caused by pre-printing treatment and washing. The development of this washing-free printing technology opens a new avenue for short-run polyester printing and contributes to improving sustainable practices in the textile industry.
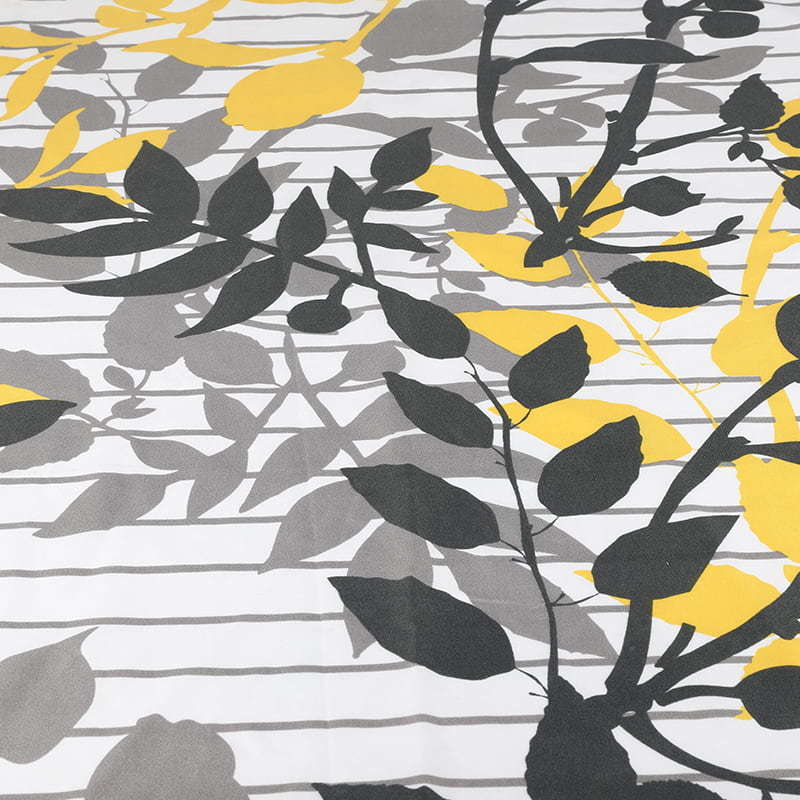
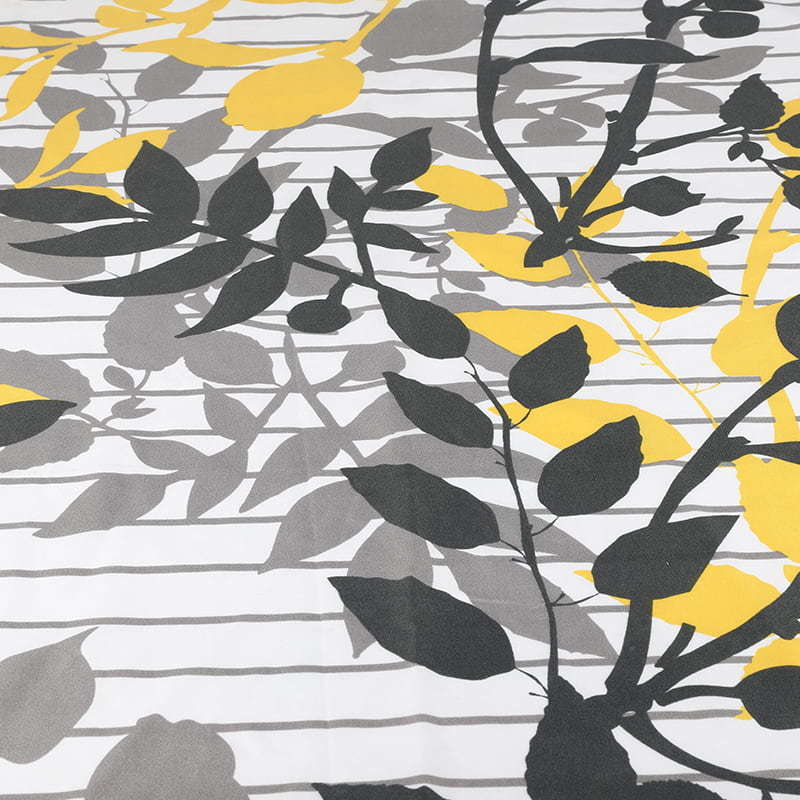